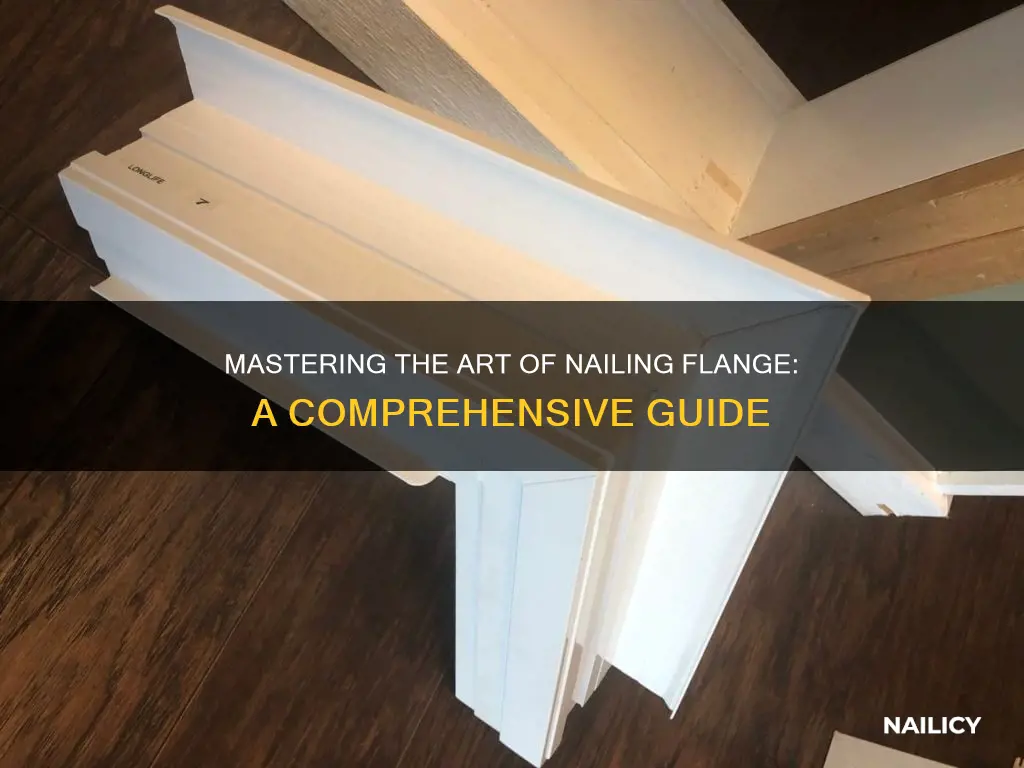
Nailing flange is a term often used in construction and woodworking, referring to a technique where a nail is driven through a flange, a protruding edge or lip, to secure two pieces of material together. This method is particularly useful for joining wooden boards, metal sheets, or other materials with a flanged edge. The process involves positioning the nail so that it passes through the flange, providing a strong and durable connection. Understanding the concept of nailing flange is essential for anyone working with materials that feature flanged edges, ensuring a secure and effective bond.
What You'll Learn
- Flange Preparation: Ensuring proper surface preparation for a secure nail
- Nail Type: Choosing the right nail for flange installation
- Angle and Depth: Optimal nail angle and depth for flange
- Nail Placement: Techniques for precise flange nail positioning
- Post-Nailing Inspection: Checking flange nail integrity after installation
Flange Preparation: Ensuring proper surface preparation for a secure nail
Nailing a flange is a specific construction technique used to join two structural elements, often in the context of metal framing or building construction. It involves securing a flange, which is a protruding edge or lip on a structural member, to another surface using nails or screws. This method is particularly useful when the flange is part of a larger assembly, such as a metal beam or column, and you need to attach it to a wall, floor, or another structural component. The process requires careful preparation to ensure a secure and durable connection.
Surface preparation is a critical step in nailing a flange successfully. The flange's surface must be clean, free from debris, and as smooth as possible to allow for a tight bond with the nail or screw. Start by removing any dirt, rust, or old paint from the flange's surface. This can be done using a wire brush or a scraper to ensure a clean and roughened surface for better nail grip. It is essential to inspect the flange and the surrounding area for any imperfections, such as sharp edges or protruding particles, and remove them to prevent damage to the nail or screw.
After cleaning and roughening the flange, it is crucial to ensure that the surface is dry. Moisture can weaken the bond between the nail and the flange, leading to potential failure. Allow the flange to air dry completely if it has been cleaned or treated with any chemicals. In some cases, you might need to apply a primer or a specialized adhesive to the flange's surface to enhance the nail's grip and provide a more secure hold.
When nailing the flange, use the appropriate nail or screw size and type for the material and application. Ensure that the nail or screw is long enough to penetrate the flange and provide a secure hold. Drive the nail or screw at a slight angle, starting from the side of the flange, to avoid splitting the material. Apply firm pressure as you drive the fastener to ensure it is seated correctly.
For optimal results, consider using a nail set or a mallet to ensure the nail is flush with the flange's surface. This step is essential for a professional finish and to prevent the nail from protruding, which could compromise the structural integrity of the connection. Proper surface preparation and the use of the right tools will result in a secure and long-lasting nailing of the flange.
Black Lines on Nails: Unraveling the Cancer Myth
You may want to see also
Nail Type: Choosing the right nail for flange installation
Nailing a flange is a specific construction technique used to secure a flange, a circular metal plate, to a structural member, typically a pipe or a beam. This process involves driving nails or screws through the flange into the structural member, creating a strong and durable connection. The choice of nail type is crucial to ensure a secure and reliable installation.
When selecting the right nail for flange installation, several factors should be considered. Firstly, the nail material is essential. Common choices include stainless steel, carbon steel, or galvanized nails, each offering different levels of corrosion resistance and strength. Stainless steel nails are highly recommended for outdoor or humid environments due to their superior rust resistance. Carbon steel nails are cost-effective and suitable for most indoor applications, while galvanized nails provide additional protection against corrosion.
The nail length is another critical aspect. Flange nails typically range from 1 to 2 inches in length, depending on the thickness of the flange and the structural member. Longer nails may be required for thicker materials to ensure proper penetration and a tight fit. It is essential to choose a nail length that allows for a slight gap between the nail head and the flange surface, providing room for the nail to expand and contract without causing damage.
Nail diameter is also a consideration. Thicker flanges and structural members may require larger diameter nails to ensure a secure hold. However, it is important to maintain a balance between nail thickness and the material's ability to withstand the nail's force. Over-driving a nail can lead to splitting or damaging the flange or structural member.
Furthermore, the nail head should be chosen appropriately. Flat-head nails are commonly used for flange installation as they provide a smooth surface for the flange to rest against, ensuring a flush finish. Round-head nails are also an option, offering a more traditional appearance but requiring careful consideration of the nail's visibility after installation.
In summary, selecting the right nail type for flange installation involves considering the nail material, length, diameter, and head style. Each factor contributes to the overall strength and aesthetics of the connection. By choosing the appropriate nail, you can ensure a secure and long-lasting bond between the flange and the structural member, meeting the requirements of various construction projects.
Biab: Understanding the Nail Treatment Process
You may want to see also
Angle and Depth: Optimal nail angle and depth for flange
Nailing a flange is a specific technique used in construction and woodworking, where a nail is driven at a precise angle and depth to secure a flange, which is a protruding edge or lip on a piece of material. This method is particularly useful for attaching trim, moldings, or decorative elements to a surface, ensuring a strong and aesthetically pleasing bond. The optimal nail angle and depth are crucial factors in achieving a secure and durable connection.
The angle at which the nail is driven is essential for proper attachment. The ideal angle is typically between 15 and 30 degrees, with the nail forming a slight incline towards the flange. This angle allows the nail to penetrate the flange's material without causing excessive damage or splitting. A steeper angle might lead to nail pop-out, while a shallower angle may result in a weaker bond. Achieving the right angle requires practice and precision, as it directly impacts the nail's holding power.
Depth is another critical aspect of nailing a flange. The nail should be driven deep enough to ensure a firm grip, but not so deep that it causes the flange to become distorted or damaged. The optimal depth can vary depending on the material and thickness of the flange. For example, a thicker flange might require a longer nail to provide adequate support. It is essential to use a nail that is long enough to penetrate the base material and the flange without leaving visible gaps or protruding heads.
To determine the correct nail depth, one can use a nail set or a depth gauge. These tools help ensure that the nail is driven to the desired level, providing a consistent and professional finish. Overdriving a nail can lead to splitting or cracking of the flange, while underdriving it may result in a weak bond. Finding the perfect balance between angle and depth is key to mastering the art of nailing flanges.
In summary, nailing a flange requires careful consideration of nail angle and depth. The optimal angle of 15-30 degrees ensures a secure bond without causing damage, while the depth should be sufficient to grip the flange firmly. Achieving the right balance between these two factors is essential for a successful and long-lasting joinery project.
Unraveling the Mystery: Horizontal Ridge on Thumbnail Explained
You may want to see also
Nail Placement: Techniques for precise flange nail positioning
Nailing a flange is a specific technique used in construction and manufacturing to secure a component, often a pipe or a structural element, to a base or a support structure. The term "nailing a flange" refers to the process of fastening a flange, which is a raised rim or lip around the edge of a component, to a surface using nails or other fasteners. This method is particularly useful when the flange needs to be positioned accurately and securely.
To achieve precise flange nail positioning, several techniques can be employed, ensuring a strong and reliable connection. One common approach is to use a layout tool or a template to mark the nail holes on the flange. This step is crucial as it ensures that the nails are placed in the correct locations, maintaining the structural integrity of the assembly. By carefully measuring and marking, you can create a straight and level line of nails, which is essential for a professional finish.
Another technique involves the use of a nail guide or a nail slotting tool. This tool is placed over the flange, aligning the nail holes with the desired positions. It provides a visual guide for the nail placement, ensuring that the nails are driven straight and at the correct angles. This method is especially useful when dealing with curved or irregular flange shapes, allowing for accurate nail positioning.
For applications requiring a more permanent solution, welding the flange in place can be an effective method. This process involves joining the flange to the base material using a welding technique, such as gas welding or arc welding. By carefully controlling the welding process, you can achieve a strong bond and precise alignment of the flange. However, it is essential to follow proper safety protocols and ensure that the welding process does not compromise the structural integrity of the component.
Additionally, when working with flanges, it is crucial to consider the material and thickness of the component. Different materials may require specific nail sizes and placement techniques to ensure optimal holding power and avoid damage to the flange. For instance, softer materials might need smaller nails spaced closer together, while harder materials can accommodate larger nails with more space between them. Understanding the material properties will enable you to select the appropriate nail type and placement strategy.
In summary, nailing a flange is a precise process that requires careful planning and execution. By utilizing layout tools, nail guides, and considering the material properties, you can achieve accurate flange nail positioning. These techniques ensure a secure and reliable connection, contributing to the overall quality and safety of the construction or manufacturing process.
Unraveling the Mystery: Bumpy Nails and Their Hidden Meanings
You may want to see also
Post-Nailing Inspection: Checking flange nail integrity after installation
Nailing a flange is a construction technique used to secure a flange, a circular metal plate, to a structural member, typically a beam or column. This process involves driving nails or screws through pre-drilled holes in the flange and into the structural member, creating a mechanical bond. The primary purpose of nailing a flange is to provide a strong and durable connection, ensuring the flange remains firmly attached to the structural element. This method is commonly employed in various industries, including construction, manufacturing, and shipbuilding, where flanges are used to join components or to provide a mounting surface for pipes, valves, or other equipment.
Post-nailing inspection is a critical step in the construction process, especially when dealing with flange installations. This inspection process involves a thorough examination of the flange-to-structural member connection to ensure its integrity and compliance with safety standards. The primary goal is to verify that the nails or screws have been driven correctly and securely, preventing potential failures or structural weaknesses over time.
When performing a post-nailing inspection, several key aspects should be considered. Firstly, check the alignment of the flange with the structural member to ensure it is properly positioned and flush against the surface. Any misalignment may indicate potential issues with the installation process. Secondly, inspect the nail or screw holes in the flange to confirm they are free from any debris or damage. Clean and inspect the holes to ensure they are ready for secure fastening.
The next step is to examine the nail or screw heads. Look for any signs of deformation, such as buckling or flattening, which could compromise the integrity of the connection. Additionally, check for any visible signs of corrosion or oxidation on the nail or screw heads, as this may affect their ability to hold the flange securely. It is essential to ensure that the nails or screws are tight and have not been over-tightened, as this could lead to damage to the flange or the structural member.
Furthermore, a post-nailing inspection should include a visual assessment of the surrounding area. Check for any signs of damage or distortion around the nail or screw holes, as this could indicate potential issues with the flange's integrity. If any defects or irregularities are found, further investigation and potential re-installation may be required.
In summary, post-nailing inspection is a vital process to ensure the long-term stability and safety of flange installations. By carefully examining the alignment, nail/screw holes, heads, and surrounding areas, construction professionals can identify and rectify any issues, ensuring a robust and reliable connection between the flange and the structural member. This inspection process contributes to the overall quality and safety of construction projects, especially in critical applications where flange connections are essential.
Unraveling the Mystery: What Light Blue Nails Symbolize
You may want to see also
Frequently asked questions
Nailing a flange is a construction technique used to secure a metal plate (flange) to a structural element, typically a beam or a column. It involves driving nails or screws through the flange and into the underlying structure, creating a strong mechanical connection. This method is often employed in woodworking and metalworking to reinforce joints and provide additional support.
Nailing a flange is a simpler and quicker method compared to welding or bolting. It doesn't require specialized equipment like a welder or a bolt gun. Nails or screws are driven manually or with a small power tool, making it a more accessible and cost-effective solution for temporary or DIY projects. However, it may not provide the same level of strength and durability as welding or bolting, especially for heavy-duty applications.
Flanges come in various shapes and sizes, depending on the application. Common types include angle iron flanges, channel flanges, and plate flanges. Angle iron flanges are used for angle-shaped connections, while channel flanges are suitable for I-beam or channel structures. Plate flanges, as the name suggests, are flat metal plates used to reinforce joints and provide additional support.
Yes, the choice of nails or screws and the driving technique may vary depending on the material being fastened. For example, when nailing a flange to wood, it's essential to use nails that are appropriate for the wood type and size. For metal flanges, self-tapping screws or specialized metal nails are often used. Additionally, the surface of the flange and the underlying structure should be clean and free of debris to ensure a secure bond.